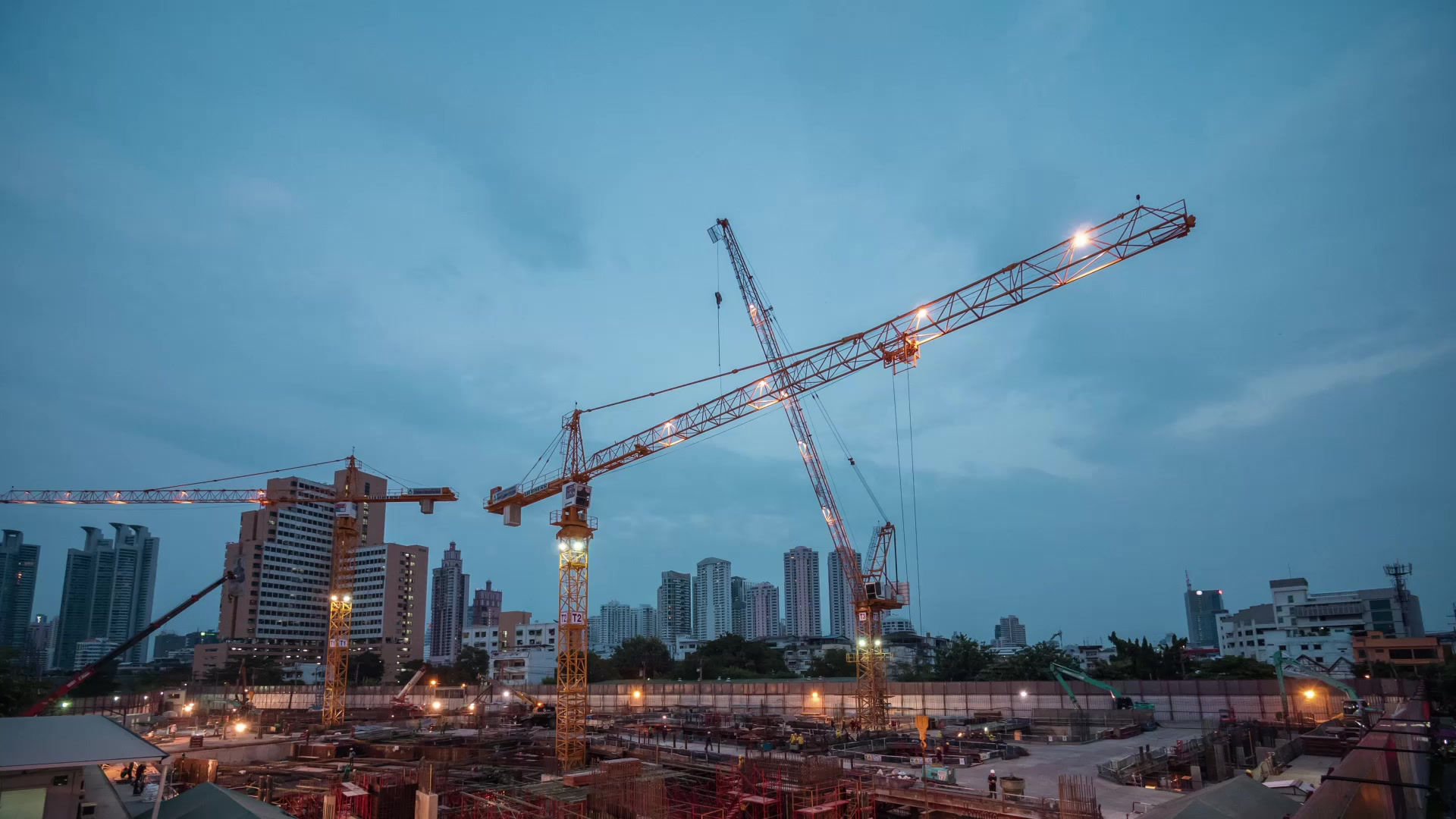
Northeast Office Building
Northeast Region, U.S.
Shawn Martin | Construction Option
Dr. Esther Obonyo
Project Info
Building Name –
Location –
Construction Dates –
Number of Stories –
Total Building Area –
Original Project Cost –
Project Delivery Method –
Occupancy Type –
Project Team
Owner –
General Contractor –
Construction Manager –
Architect –
MEP Engineers –
Structural Engineers –
Northeast Office Building (fictitious name)
Northeastern Region of the United States
September 2015 - March 2018
9 (Including Attic and Basement)
220,000 SF
Approx. $61
Design-Bid-Build w/ CM Agency
Business and Office
General Services Administration https://www.gsa.gov/
Gilbane Building Company http://www.gilbaneco.com/
Grunley Construction http://www.grunley.com/
Jacobs Engineering http://www.jacobs.com/
CallisonRTKL https://www.callisonrtkl.com/
JVP Engineers http://jvpengineers.com/
Silman http://www.silman.com/
Architecture
The architecture of the building is described as neoclassic, maintaining consistency with the surrounding structures and buildings. This is resembled in the massive Doric columns positioned on parts of all four sides of the building. Construction broke ground in the 1920s and was completed in the early 1930s. The building is rectangular, occupying multiple city blocks, measuring near 300 feet east to west and over 1000 feet north to south. While all four sides of the building have multiple entrances, the grand entry is centered on the east side of the building. Broken up into corridors, the building contains more than 3,300 offices and rooms. The corridors gives way for 6 interior courtyards, providing natural daylighting and ventilation. Due to the occupancy type and owner of the building, it is considered to be unzoned and does not require zoning regulations. This building is limited to height restrictions due to laws in the area. One of the laws limits the building height to be no more than 160 feet in this area. Due to the site location, the Northeastern Office Building does fall within a national historic site. This historic area several historically significant structures that have played a substantial part in American culture. As this building is considered historical, one of the challenges of renovating was to keep certain aspects and parts unscathed as a requirement of historical sites.
General Building Data
Applicable Codes
Phases 1 through 4 of the Northeast Office Building must abide by the International Building Code (IBC) 2006, unless established to further adhere to a more recent International Building Codes. All systems must follow the most current respective codes to date (2015): National Electric Code (NEC), International Fire Code (IFC), International Mechanical Code (IMC), and the International Plumbing Code (IPC). The project is also designed to comply with the certification level according to the U.S. Green Building Council’s Leadership in Energy & Environmental Design Rating System.
Building Enclosure
The façade of the building is a gray Indian limestone mounted on a granite bases, which will remain due to its historical status. The existing windows have been deemed inoperable and the renovation calls for abatement of all existing windows. Also, the renovation includes installation of new Therm-O-Lite Blast Resistant Windows on all exterior facing locations and Therm-O-Lite Thermal Windows on all interior facing locations. These windows are to be framed and installed on the inside of the existing windows to maintain the historical presence. The roofing of the building utilizes clay roof tiles with sheet metal flashing/counterflashing and roof-expansion-joint covers. These materials are to remain existing unless evaluated as a risk to the integrity of the building.
Sustainability Features
The renovation will replace all major MEP systems within the building and follow the LEED for New Consturction & Major Renovations V2.2 to attain a Silver LEED rating status. This will include government initiatives to increase building and perimeter security, a higher performance workplace design, as well as energy efficient building systems. Construction will also consist of green constuction practices for Materials & Resources to monitor and limit waste during the renovation. This embraces recycling of existing materials to limit its carbon footprint.
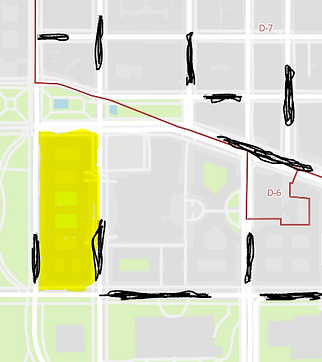




Exterior Wall Detail
Typical Roofing Detail


Construction
The Northeast Office Building project is a renovation job to modernize the 1.9 million square foot business and office building. Owner of the building, General Services Administration (GSA), established a plan in 2008 to upgrade critical building systems, restore interior aesthetics, and improve structural deterioration. The proposed renovation was divided into 8 phases spanning over 13 years, and is estimated to cost $750 million. To date, Phase I, II, and III are substantially completed. Phase 4 is currently in progress and is projected to reach substantial completion in December of 2017.
With the Northeast Office Building being recognized as a Historical Landmark, GSA became aware of the visible “wear and tear” in the early 2000s and set out to create a modernized office building. This renovation was set to improve the building’s inefficient workplace layout on top of the outdated building systems. GSA also had concerns about the health hazards the building contained which included asbestos and lead-based paint. This renovation would allow for continued growth and an improved work environment within a major government building.
To accompany the thousands of workers the building houses, GSA created an 8 Phase project schedule, allowing the building to remain in use during construction. The phases were broken down into roughly equal sections (around 15% of the total building area per phase), minimizing disturbance to day-to-day activities held in the office building.
GSA required the Northeast Office Building renovation to be carried out as a Design-Bid-Build Project with utilization of a CM Agency. Jacobs Engineering was hired as the Construction Management Agency by GSA due to the large project cost and lengthy schedule. Also due to the magnitude of the project, it was carried out as Design-Bid-Build. This establishes an early period for design, prior to construction taking place. During the bidding stage, Gilbane Building Company and Grunley Construction won the job as a joint. This bid awarded Gilbane-Grunley Phase I through Phase IV of the project, with the potential to be awarded the following phases based on performance. This joint venture combines the specialized abilities of Grunley in the government construction sector with the large general contractor services of Gilbane. This allows the risk to be split between the entities, combination of expertise, and the spread of bonding capacity. Prior to Phase 4, GSA brought on board CallisonRTKL, JVP Engineers, and Silman as the architect, MEP engineer, and structural engineer respectively. These firms held responsibility to the design completion for the 220,000 square foot Phase 4 and GGJV holds a GMP value of roughly $61 million for this phase.
Electrical
The electrical system is being demoed and upgraded. Four (4) medium voltage (13.8 kV) switchgears will be housed in the penthouse, feeding the Phase 4 area. The main switchgear will also have medium voltage (13.8 kV) generators paralleling the switchgears to increase reliability and for uninterruptible maintenance. A medium voltage (4.16kV) switchgear will also be installed in the penthouse to supply power for the chillers. Additionally, a low voltage 480V switchgear will be installed feeding power to several utility busways throughout the building. Main distribution feeders span from reach up to 2000 amps, using at most a 600 kcmil wire.
Lighting
The lighting system will see upgrades to all existing interior lighting fixtures, lamps, ballasts, emergency lighting units, exit signs, lighting fixture supports, and retrofit kits for fluorescent lighting fixtures. Interior historical lighting will seek restoration with new custom lighting fixture that match the existing historic fixtures, lamps, ballasts, materials, and supports. All interior lighting shall comply with LEED EARP1, EA1, and ID1.4 requirements. Low-mecury lighting shall be used to comply with LEED innovation credit and the mercury content for all lamps should maintain an average below 80 picograms mercury per lumen hour. Exterior lighting will see the same upgrades in regards to the historical lighting system. Most office, conference rooms, bathrooms, corridors, and lobbies will now use LED.
Mechanical
A majority of the contract’s scope of work is emphasized on renovating the building’s mechanical system. Existing AHU’s, piping, ductwork, diffusers, controls, chillers, pumps, chilled/hot water supply and return, and any and all appurtenances are to be demoed and upgraded. Phase 4 scope includes the installation of 8 AHU’s, ranging between 4,500 and 22,000 CFM. These AHU’s will be house in mechanical rooms in the basement, 2nd, and 6th floors. Two 2,000 ton and one 800 ton water-cooled-centrifugal chillers will be installed in the basement. Also installed in the basement will be four shell & tube and one water-side economizer hot water heat exchangers. Throughout the interior office areas, over 300 window and wall FCU’s will be installed functioning as the domestic air supply for typical work spaces.
Structural
The existing structural steel frame consists of steel girders supporting the slab on deck and columns that are encased in concrete. This renovation has minimal focus on the structural steel of the building, as the existing system is to remain. The scope of work includes structural steel erection for the 8th Floor Penthouse. This area is to house mechanical units, switchgears, and transformers. The existing structure in this area is not designed for the new equipment, thus requiring additional steel girders for support.
Cast in place concrete is also a limited addition to the building during renovation. Due to the high capacity of renovation of mechanical systems, many floors require penetrations of the floor slabs. After the mechanical equipment is installed, the concrete contractor is to cast in place these mechanical infills, utilizing traditional lumber formwork. Subsequent floors require shoring and post-shoring during this stage to maintain structural stability. Additionally, a new slab is to be poured on the existing slab in the 8th Floor Penthouse Mechanical Room and the Basement Chiller room. To achieve LEED Silver Certification, the owner is requiring the contractor to use recycled-content materials, locally-manufactured materials, low-emitting materials, construction waste recycling, and the implementation of a construction indoor air quality management plan.
Primary Engineering Systems
Additional Engineering Systems
Demolition
The Northeast Office Building was constructed in the late 1920s. With this project being the first major renovation of the building, one priority of this project is the abatement of hazardous materials (lead-based paint and asbestos). Within the Phase 4 scope, all interior building areas and all exterior windows must be tested and abated. In regards to Asbestos Containing Materials (ACM), the scope mainly includes (but is not limited to) the abatement of pipe insulation, pipe hangers, mudded joints, mastic on metal ducts, flooring materials, acoustical ceiling plaster, window caulking, wall tile, spray-on fire proofing, and duct insulation. In regards to lead-based paint, the abatement contractor is to demo all positively-tested surfaces included in the test results taken by MACTEC, reported on April 18th, 2003. MACTEC’s report contains 1,115 XRF (X-Ray Fluorescence) tested areas, having 85% of the readings detecting 0.10 milligrams per square centimeter of lead-based material.
Fire Protection
In regards to fire suppression, the wet-pipe systems will be receiving a large upgrade with new risers, valves, gauges, alarms and other amenities. Limited areas in the building utilize a dry-pipe system, but these areas will receive no upgrade.
Transportation
Existing elevators and system are to remain. The elevators will be restored and refurbished per the same scope from Phase 3. During construction of Phase 4, the West Corridor elevator will be completely out of use. The East Corridor elevator will be used as a means of transportation for laborers and materials on site.
Telecommunications
Common work for telecommunications includes; grounding and bonding for systems, hangers/supports, conduits, backboxes, non-metallic tubing with fabric innerduct, cable trays, termination blocks, patch panels, cable management, ladder racks, copper backbone cabling, copper cable splicing, optical fiber backbone cabling, copper horizontal cabling, optical fiber horizontal cabling, faceplates, connectors, patch cords, station cords, and cross connect wiring. The structured cabling system (SCS) must serve as a vehicle for transporting data, video, and voice telephony signals throughout the network from demarcation points to outlets at desks, workstations, among other locations. The applications and link standards must include IEEE 802.3-2002 (Ethernet), 1000BASE-T (Gigabit Ethernet), TP-PMD (Copper-based FDDI), 52/155 Mbps ATM (asynchronous transer mode, and 77 Channel Analog Broadband Video out to 550 MHz). The Gigabit Cable Performance must be capable of support applications including AES/EDU Digital Audio, 270 Mbps Digital Video, 622 Mbps 64-CAP ATM, 1000Base-T Gigabit Ethernet and 1.2 Gigabit ATM.